Modular construction, a method where building components are manufactured in factories and assembled on-site, presents a compelling solution to several challenges faced by the US construction industry. Modular construction is poised to revolutionize the sector with the ability to address issues like high material prices, disrupted supply chains, and shortages of skilled labor. Despite its evident advantages, the broad acceptance of this approach in the US could be more active. According to a recent study by McKinsey & Company, it is revealed that modular construction accounts for less than 4 percent of the current housing stock, a stark contrast to the higher percentages observed in other countries.
The hesitance to embrace modular construction in the US is rooted in challenges related to the interfaces between modular companies and the broader construction ecosystem.
1. Overdesign:
Modular buildings thrive on standardization for efficient series production. However, designs that are robust enough for every application tend to be over-engineered. This can inflate material costs. Modular companies can employ design-to-value techniques to address this, optimizing features and material specifications for individual modules during the pre-production design phase.
2. Inefficient Installation:
Due to the novelty of modular construction in the US, on-site contracting teams may need more familiarity, leading to potential inefficiencies. To combat this, leading modular companies invest in project-management capabilities, hiring experienced industry professionals to oversee projects, work with contractors, and continually refine products and processes.
3. Insufficient Capital:
Modular construction is capital-intensive, and the perceived risk compared to traditional methods makes it challenging to secure financing. To alleviate this, modular firms can work with finance partners to develop phased bonding approaches, releasing project bonds in stages tied to manufacturing milestones.
4. Unsteady Manufacturing Pipelines:
Construction’s inherent variability can disrupt production line efficiency. Modular players can address this by adopting collaborative business development strategies, using analytics tools to understand regional construction costs, and establishing long-term strategic relationships with stakeholders for a healthier pipeline of future work.
5. The Weakness of Isolation:
Isolating modular players from early collaboration with designers and contractors hampers project outcomes, limiting innovation and inflating costs. More than relying on singular approaches leads to missed opportunities. Collaborating with designers, general contractors, and major customers can increase bid-win rates by developing partnerships with general contractors, ensuring alignment and strategic collaboration throughout projects.
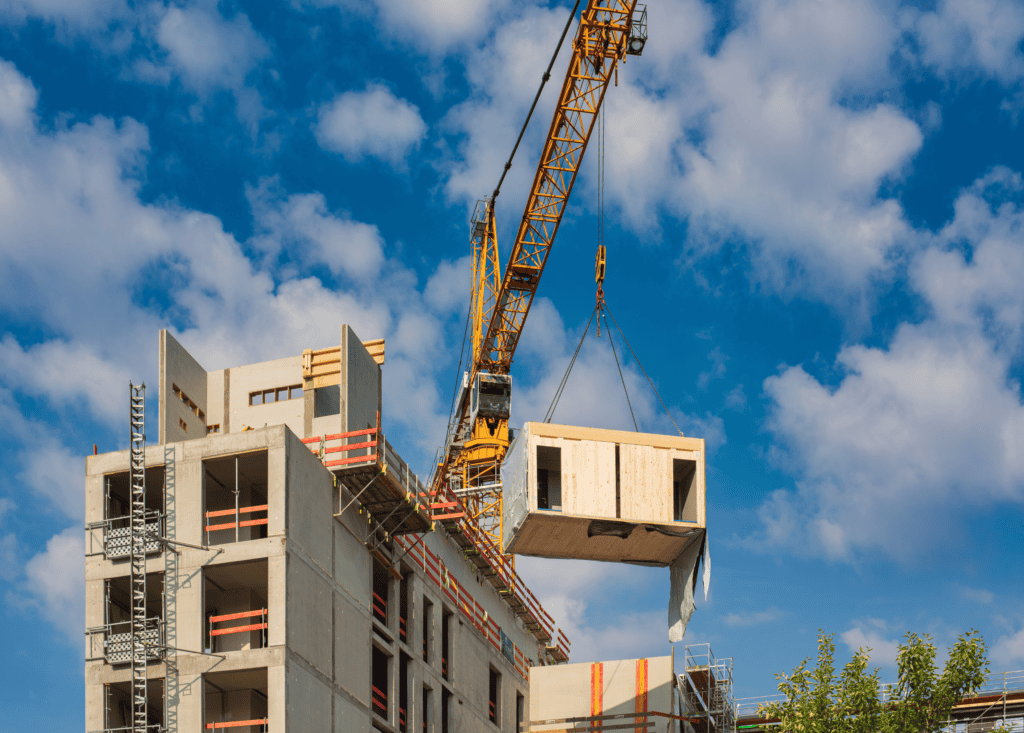
Overcoming these challenges could unlock accelerated growth for the modular construction sector in the US, benefitting not only the industry but also the broader society. Developers and general contractors stand to gain from faster project execution, higher margins, and increased competitiveness, especially in environmentally conscious regions. Cities and states, in turn, could leverage modular techniques to produce more affordable housing on smaller, safer construction sites, creating opportunities for a diverse skill base. For modular construction to truly become a competitive alternative, fostering strategic alignment and shared financial benefits across the construction ecosystem is crucial, a collaborative approach that promises to reshape the future of construction in the United States.